熱処理を検討する前に設計屋さんが知っておくべきこと
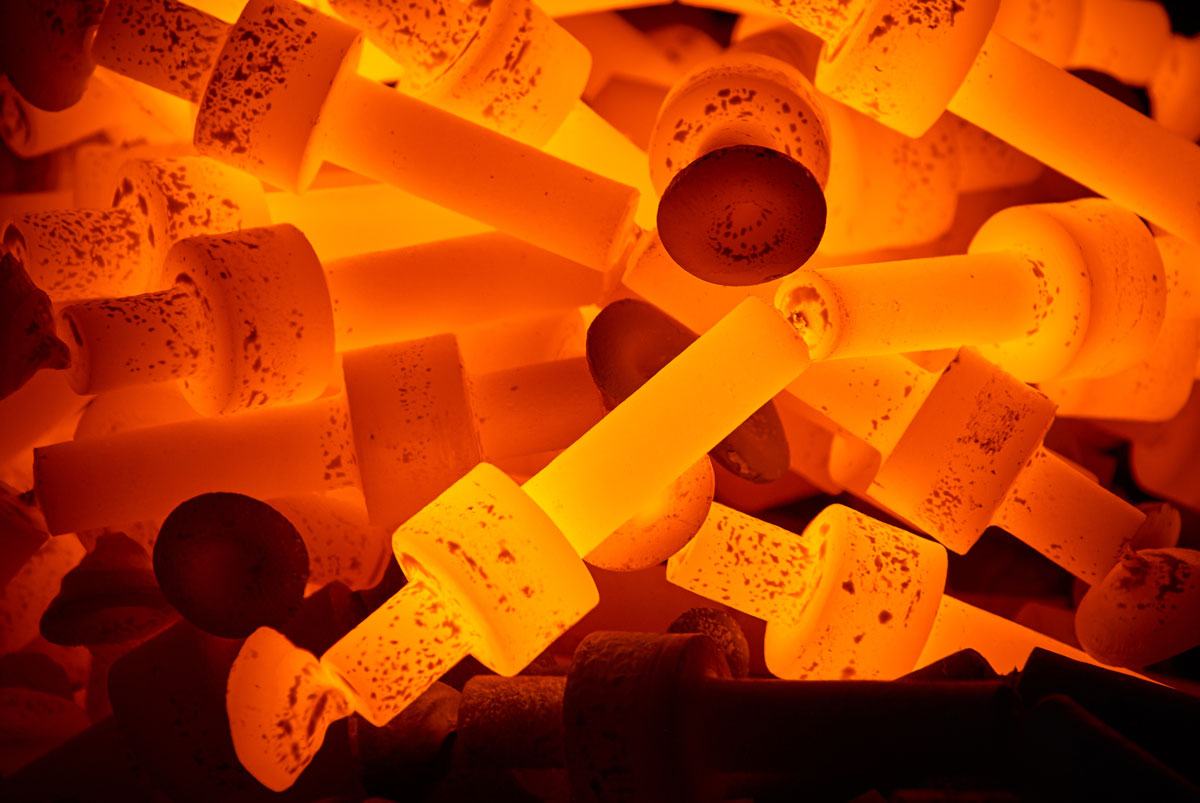
「要求されている硬度を出すために熱処理をかける」金属加工においてごく一般的な考え方です。
しかし、加工図面を引く段階では、意外と熱処理をかけることによる影響を見落とされてしまうことが多いです。
図面を引く際に「この金属に熱処理をかけることでどうなるのか」ということをしっかりと考慮しておかないと、熱処理による変形や膨張の手直しに余計な工数やコストが発生してしまいます。
本コラムでは、難削材の高精度加工を長年手がけてきた経験を元に、
- 設計屋さんが知っておくべき熱処理の注意点
- 熱処理以外の硬度を出すための方法
といった点を解説します。是非ご一読いただき、よりよい設計にお役立てください。
設計屋さんが知っておくべき熱処理の注意点
熱処理を検討する際には「熱処理をすると金属は変形する」という前提を忘れてはいけません。
近年では、様々な熱処理技術が開発されし、変形を抑えた熱処理が可能になっています。しかし、金属に熱を加えて処理する以上、大なり小なり変形は発生します。
素材によって、熱処理で寸法が変わりやすいもの、変わりにくいものに差が出ますし、切り欠きやオープン形状(コの字、U字など)、片面だけを大きく削り込んだ部品など、加工形状によって膨張の仕方も変わります。
熱処理で硬度が増した金属が変形、膨張すると、仕上げに高硬度用の刃物が必要になります。
高硬度用の刃物は摩耗も激しく、精度も出にくいため、仕上げ工程に膨大な工数とコストがかかってしまいます。
特にS45CやSK材は熱処理による変形を起こしやすい金属です。
熱処理後に公差を維持できるか、NAK材などの材料変更はできないかといった点を設計段階で考慮する必要があります。
当社にご相談いただく図面には、熱処理・表面処理後の寸法が書かれているものも多々あります。
こういった図面は言わば設計者にとって都合のいい描き方をされた図面であり、図面に描かれた公差を維持するため、加工や仕上げで工数、コストがかかってしまいます。
加工のトータルコストを最適するために、設計段階から熱処理による変形を考慮しましょう。
熱処理以外の硬度を出すための方法
金属の硬度を出すための方法は熱処理だけではありません。
本章では、金属に硬さを持たせるための様々な手法について解説します。
①ハードクロム
めっき処理の一種で、金属を溶かしためっき液にワークを浸し、皮膜を作ることで硬度・耐摩耗性・耐熱性を付与することができます。
製品の形状によっては治具が必要になる場合もあり、処理中にクラックが発生しやすい点にも注意が必要です。
②ショットブラスト
投射材と呼ばれる粒体(砂や鉄の小球)を吹き付けてワークに衝突させて加工する手法です。
主にバリの除去や表面研削に用いられますが、金属の表面に残留圧縮応力を付与させることで強度、耐応力を向上させることもできます。
吹き付ける投射材の種類や、投射方式(機械式、空気式、湿式)によって得られる効果が異なります。
表面に粒体を吹き付けるという処理の性質上、高い精度の表面粗さが必要な製品には不向きとなります。
③窒化処理
金属に窒素を浸み込ませて表面を硬化させる手法です。
焼入れや焼戻しなどの熱を入れる工程がないため、金属の変化が極めて少ないという特長があります。
窒化の種類によって、処理可能な金属とできない金属がある点に注意が必要です。
④材質そのものを変える
NAK材など、熱処理しなくても高い硬度を持つ素材に切り替えることも有効です。
近年では超硬材の加工技術も発達し、高い硬度を持った部材を高精度で切削することも可能になっています。
このように、金属の硬度を出すためには熱処理以外にも様々な方法があります。
製品の仕様、要求される硬度、納期やコストなど、様々な条件から最適な方法を見出すことが重要です。
ときには製品にその硬度が本当に必要なのか、という根本的な問題に立ち返ることも大切になります。